Blog
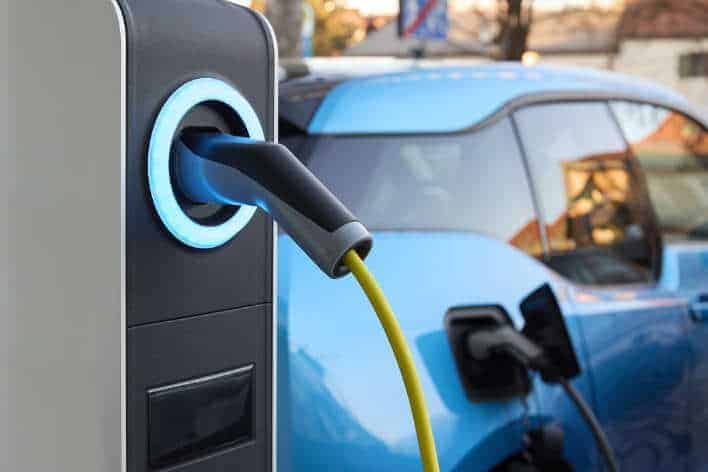
08Sep |
Introducing the new CST Spotlight blog series: This month we shine a light on Northwest Power (Vicor Corp)
Series introduction: Over the past year, I’ve dedicated several of our blogs to recognizing and promoting the importance of investing in electronics infrastructure in order to maintain our technological leadership, global competitiveness, and national security – whether those investments take the form of STEM efforts, government incentives like the CHIPS and Science Act, supporting the R&D tax credit, or public/industry collaboration. Not coincidentally, I’ve also tried to spotlight the importance of all levels the electronics ecosystem, including major semiconductor manufacturers; printed circuit board, component, box assembly, and packaging companies (like our own firm, CST); and countless adjacent players like software developers, contract manufacturers, testing labs, consultants, among many others.
With this new “CST Spotlight” series, I’m excited to shift to real-world examples of innovation happening within CST’s own sphere – by drawing attention to the noteworthy breakthroughs being achieved by our customers. (I’m also proud that CST is helping them in our way, as a supplier!)
Hope you enjoy these conversations and that you’ll let me know if you do!
– Shantanu R. Gupta,
CEO, Cascade Systems Technology
At this point, it’s clear that a well-conceived technology roadmap and a growth plan for electric vehicles (EVs) will drive the future of clean tech and impact our civilization and, indeed, our planet. Fortunately, there are companies like CST’s customer Northwest Power (NWP), a subsidiary of Vicor, who are hard at work overcoming some of the most pressing challenges of EV design. As the company’s website puts it, they are “a leader in high-performance power modules, enabling customer innovation with easy-to-deploy modular power system solutions for power delivery networks.” Recently, I had a chance to speak with Chris Roots, who is Director of Operations at NWP’s Milwuakie, Oregon facility about some of those challenges and what his firm is doing to surmount them.
Q | SHANTANU GUPTA: Chris, thanks for connecting with me on the exciting things you’re working on at the moment in the automotive sector, where we’ve had the opportunity to support you and collaborate with you and your team. Can you touch on a couple of the challenges that have got your gears turning at present?
A | CHRIS ROOTS: Thanks for including us in the CST blog; it’s been a pleasure working with your team on a variety of projects in recent years and I’m happy to share some of the things we’re seeing in the EV industry based on work we’re doing for several of our own customers. The first is the fact that EVs are still running a 12V accessory circuit, and most have a traditional 12V battery in them to power all the traditional parts such as radio, headlights, wipers, power seats, electronic steering, and so on. There is typically an HV-to-LV charger that uses the HV battery to keep the 12V battery topped up. This is clearly not the most efficient way to get power to these items, but since the legacy 12V system is so deeply ingrained and ubiquitous in the automotive industry, and since designing an EV already takes so much engineering time, it just makes sense for these first-gen EV cars to use the existing 12V parts that are so available.
Q: So, how do you see the industry addressing this or migrating to another approach? And what will that new approach look like in future models of EVs?
A: The first step we’re seeing on the path away from 12V is to eliminate the battery, and use real-time, on-demand power conversion from the HV battery pack to 12V. It’s a small step from the perspective of the whole car, but the power supply design is challenging in that the response time to dramatic changes in current on the 12V end must be very, very low. The primary example of this would be emergency maneuvers that include large brake and steering inputs. If there is a lag in the power delivery to the braking and steering system due to the large transient in current, bad things happen. Of course, overall reliability is very important as well. Losing 12V while driving down the road would be unacceptable.
Q: Talk about ways that system designs can positively or negatively impact consumers in the real world! What’s the next step?
A: After replacing the 12V battery with on demand power conversion, we’ll need to change whole accessory architecture – as opposed to the drive architecture — to a higher voltage, probably 48V. The on-demand power supply can easily be redesigned to output 48V instead of 12V, and the conversion efficiency increases quite a bit at 48V vs 12V. Bussing 48V around the vehicle instead of 12V also has the advantage of being 1/4th the current of the 12V system, given the same power. So, the lower current directly translates to smaller wires and less losses over length. And as LV power consumption increases in future vehicle designs, the gains of a 48V bus will increase as well.
Q: Sounds promising, more efficient for sure, with lots of trickle-effect benefits. What else are you and Northwest Power working on?
A: The second problem we’re working on is the switch from 400V batteries to 800V. Up until this model year, I believe, all EV manufacturers were using 400V battery packs because that is what was available. 800V battery packs are now becoming production ready and I think Hyundai is the first to hit the market with an 800V platform. I won’t go into the benefits of the 800V over 400V, but again the 50% reduction in current for the same power is not inconsequential. The issue that has been brought to us is the fact that EV charger infrastructure that so many businesses are pouring money into right now is almost all 400V chargers. As 800V platforms become more common, 800V chargers will also become more commonplace, but the 400V chargers and 400V cars will still be out there.
Q: That will sort of put some onus on consumers, won’t it? Knowing what charging system is a fit for their vehicle… Like gasoline vs. diesel?
A: Yes. Asking drivers to not only know if their car is 400V or 800V, but also paying attention to charger voltages is probably not conducive to the EV adoption rate that manufacturers are wanting. One solution is a bi-directional 400V<->800V converter that can output fast charger power (150kW or so) and can be installed one way in 800V cars, such that if they plug into a 400V charger it steps it up to 800V, and installed the opposite way in a 400V car, so that if connected to an 800V charger it will step it down to 400V. This is the solution we are currently working on.
Q: Some interesting challenges and trends to keep an eye on for sure. And no doubt Northwest Power, and Vicor, are encountering analogous or even more complex power-handling challenges in rail, UAVs, space vehicle, and even – let’s call them stationary applications as well, like robotics and manufacturing automation?
A: Oh yeah, that’s really our core competency. We’re always looking to achieve gains in density, efficiency, power-delivery capabilities and packaging… The same things we and no doubt your other customers demand of you, Shantanu. Everyone wants it smaller, lighter, with better thermal properties, more reliability, and cost efficiency.
Q: It’s what we do, right?
A: It’s what we do. And all of these solutions require a competent, collaborative, responsive PCBA partner like CST that enables Northwest Power & Vicor to design, build and test out these innovative solutions that are moving the needle for this exciting industry!
SHANTANU: Thanks Chris! It’s indeed our pleasure to have the opportunity to partner with an industry leader like yourself.
Interested in learning more about what Northwest Power is up to at the forefront of power management or the kinds of solutions CST is contributing to the effort – email Chris or email me a line at CST.
– Shantanu R. Gupta,
CEO, Cascade Systems Technology
Are You Ready to Get Started?We have a team of customer service experts ready to assist you today! |