Blog
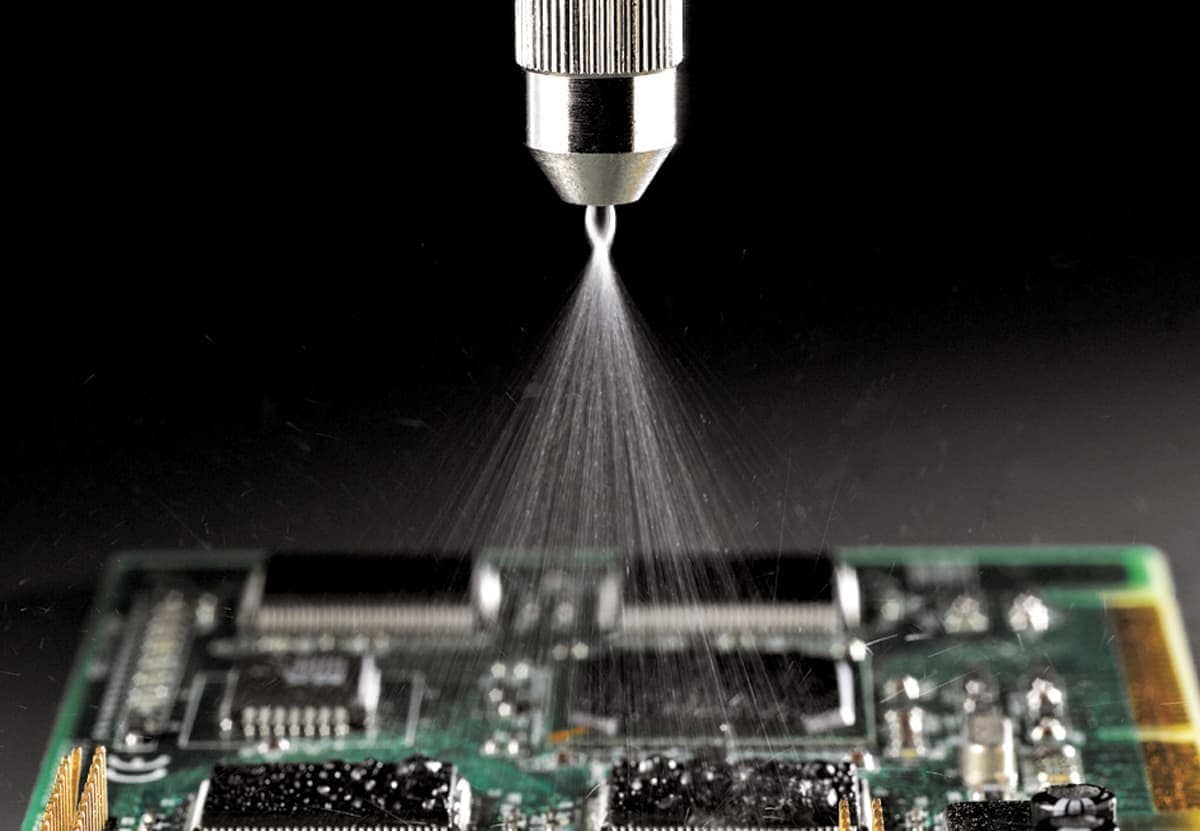
17Jan |
Here’s what you should know about conformal coating.
Over the holidays, I had occasion to watch a National Geographic documentary on the April 2019 fire that took place in the Notre Dame cathedral in Paris. A segment of the show touched on how the city fire department utilized an unmanned, 1,110 lb. fire-fighting machine, lovingly called the Colossus, to enter parts of the inferno unsafe for human firefighters. Not only was this advanced unit charged with discharging 660 gallons of water per minute into the blaze and providing a live video feed and sensor data to provide valuable insights on the fire’s progress to nearby fire chiefs – it had to perform these and other duties under the duress of incredible heat, drenched in water, and withstanding various impacts and vibration from falling or fallen debris, including molten lead from the cathedral’s lead roof. Talk about hostile workplaces!*
* You can read more about and see the Colossus in action, here.
Needless to say, the story brought to mind the advances the electronics industry has made and continues to make in the arenas of mobility, connectivity, processing, and – especially in this instance – durability. After all, machines like this don’t just happen: From major systems, to sub-assemblies, to individual components, on down the line — they are painstakingly designed, spec’d, and built to perform in adverse conditions.
Which brought to mind the increased importance of the protection afforded by conformal coatings.
What is conformal coating?
Conformal coating involves spraying or immersing a printed circuit board (PCB) or PCB assembly in a protective coating – in much the same way that a car manufacture or service shop applies a coating undercarriage of your car. The applied material ‘conforms’ to the irregular surface or landscape of a PCBA, including surface-mounted components, solder points, raised or etched circuits, component leads, through-holes, and more. Once applied, applied conformal coatings must dry or cure for a suitable period of time before additional processing, assembly, quality control, or other tasks can proceed. Once applied, such coatings can protect against any number of strains your circuit may encounter in the real world, including:
- Moisture, oils, chemicals, solvents
- Thermal stresses, including extreme heat and cold
- Vibration, abrasion, physical impacts, handling during shipping, regular use, or service
- Dust, dirt, grime
- Ultraviolet (UV) exposure and degradation
- Unexpected electric shocks (transient voltage surges, aka: lightening), shorts, and static electricity
- Radiation
What are conformal coatings made of?
Conformal coatings or ‘resins’ come in a variety of compositions to match your unique application or performance goals. While other materials are available, including a new breed of ‘nano’ coatings, the three major types of traditional coating material options are:
- Apoxy Resin (AR) is a rigid coating that offers basic, low-cost dust and moisture protection. Apoxies are, though, susceptible to chemical solvents, which makes it easier to intentionally remove the coating to do rework and field repairs easier, even if it also makes them less-than-ideal for caustic industrial settings.
- Silicone Resin (SR) is a flexible, hydro-repellent material suitable for high-vibration and/or outdoor environments. SR-based coatings also have excellent dielectric properties, so they can help isolate high-voltage (aka: eliminate arcing) or, inversely, help protect static-sensitive components or PCBAs.
- Urethane Resin (UR) is a hard coating that offers even better moisture and chemical resistance than SR- and AR-comprised coatings, which makes them a frequent choice in mission-critical aerospace, defense, avionics, or medical applications.
Key considerations of conformal coating
For a material that measures only 1-5 microns in thickness – the particulars of conformal coating composition, characteristics, and application require a deeper discussion than this blog post allows. That said, I can say choosing the right conformal coating for your unique application can be guided by five high-level considerations:
- What kind of protection do you require? As outlined above, different conformal coatings offer different levels of protection. To pick the right one for your project, list and rank your priorities – permeability to moisture, chemical resistance, dielectric performance, ability to withstand or adjust to thermal contractions/expansions, vibration, and so on – and then work with your PCBA supplier to choose the right one for your job.
- What sort of production process or timing are you working with? Are you working with small volumes where application of the coating can be manual, or high-volume runs that demand automation? Can your production schedule withstand long or short conformal coating curing times? What sort of quality system regimen do you or your customer demand to ensure repeatability? These and other production and process aspects should be accounted for when choosing your conformal coating.
- Speaking of QA, will your PCB, assembly, or finished device have compliance requirements? Individual customers may have proprietary specs or requirements, but most applications for conformal coated PCBs and PCBAs are commonly assessed against two prominent, namely IPC-CC-830B (or MIL-I-46058C) and UL746E.
- Will the end device or equipment require rework or even allow for in-the-field repairs? If so, some coatings are better suited than others.
- What’s the budget? No surprise that a hard-nosed cost/benefit analysis will be needed in choosing your conformal coatings, just as it does with every other item on your BOM. Thankfully, the wide range of conformal resins, application techniques, and suppliers – and availability of emerging coating options – all but ensure there is an option to suit your task without too many trade-offs.
Which applications require conformal coating?
The length of this blog here again precludes an exhaustive analysis of environments and applications that would benefit from resin-coated electronics. Still, my opening story of the Colossus fire-fighting machine makes clear some emerging applications are particularly well-suited to ruggedized electronics enabled by conformal coated circuits. For instance:
- Unmanned vehicles – Robots with fire-fighting capabilities are just the beginning of this fast-growing field. (Come to think of it, I wonder if any were or could have been used to save lives and property during the Oregon wildfires that plagued CST’s own region last July?) Similar equipment is being applied in mines, sites of industrial accidents, war zones and law enforcement applications, and deep-sea, arctic, and space exploration, among other extreme environments.
- Internet of Things (IoT) – Enabled by nearly ubiquitous broadband access (including 5G), connected sensor networks, and insatiable demand for/insights from big data and machine learning are also driving electronic devices into harsh and remote environments: Think of far-flung water, gas, and oil pumps; all-season sensors deployed across forests, farm fields, and water systems; traffic, vibration, and erosion sensors dispersed across interstate highways, bridges, rail systems, and cityscapes.
- Communications infrastructure – Having mentioned how communications networks are drawing IoT technology into challenging environments, the same can be said for the infrastructure comprising those networks themselves. Base stations, cell towers, satellite dishes, antennae, mobile wireless equipment, and even satellites are subjected to a wide range of environmental stresses, making them key candidates for conformal coatings among other protective measures.
- Handheld technology – Aided by miniaturization, innovative packaging solutions, and IoT connectivity mentioned above, handheld devices and other types of portable equipment are also driving technology into environments requiring ruggedization techniques like conformal coating. Two examples of this trend would be mobilized medicine and laboratories that bring healthcare and science into ever more remote challenging geographies — and app-driven handheld tools that enable industrial technicians to perform in-the-field maintenance, diagnostics, and even repairs.
Need conformal coating? CST is here to help.
In addition to assisting you with design and manufacture of your PCBA, Cascade Systems Technology has the experience, expertise, and infrastructure to help you choose, engineer, and apply the optimal conformal coating for your unique application. From small runs dictated by complexity or by production-on-demand schedules – to continuous, high-volume runs requiring high levels of automation – CST has your PCBA and conformal coating needs covered! Contact me to discuss the possibilities, CST’s capabilities, or initiate a quote.
– Shantanu R. Gupta,
CEO, Cascade Systems Technology
Are You Ready to Get Started?We have a team of customer service experts ready to assist you today! |